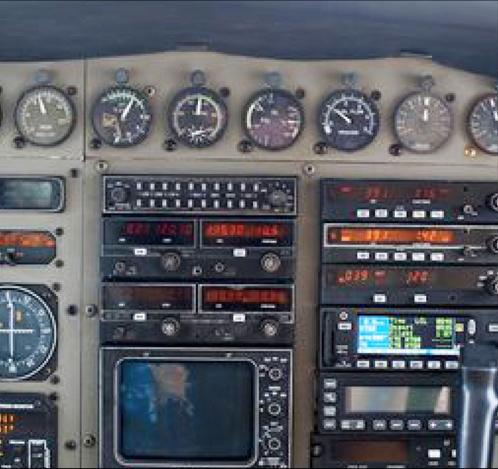
One of our key operations is the reverse logistics processes. We handle the repair and return of parts, assemblies and systems with quality and efficiency while we track all internal processes.
Whether parts are electronic or mechanical, we use learned lessons from modern approaches of world class manufacturing and repair, and use the latest equipment and automation software. Our repair and return approach allows us to achieve results at a top level of quality and at an optimal cost. We have engineered automation into our processes to maximize the turnaround speed of all repairs, yielding significant cost savings to the customer.
The repair and return processes comprise the following key areas:
Repair & Return Tracking Software
Ensures that we accurately determine the status of all repair assemblies from the receiving end to the return to the customer. Tracking software enables us to track repair status, delivery time and cost in real-time.
Automated Repair process
Our engineering staff develops instrumentation and software systems that take out guessing and human errors out of the repair process. Each part or assembly of an electronics system is tested with modern automated instruments under the direction of software containing engineered algorithms, test sequences, and pass and fail parameters, which provides diagnostics for a failed unit.
Sub-assembly exchange
Failed units are replaced using our exchange process. We maintain inventory of the most common parts and sub-assemblies so that we can rapidly repair most systems. The failed sub-assembly then is separately repaired so that it will not affect the delivery time to the customer. In this manner, critical assemblies will be returned quickly and high-value products and parts will not sit waiting to be repaired for a prolonged period of time. This approach reduces significantly the cost, and enables the customer with the readiness needed to reliably maintain field operations.